Guardian Industries przekształca – ciągłe doskonalenie
W Indianie Guardian Industries wykorzystuje pojazdy autonomiczne, aby usprawnić swoje procesy, stworzyć bezpieczniejsze środowisko pracy i zapewnić większą spójność dostaw materiałów do swoich gniazd roboczych.
Od kilku lat branża transportu materiałów, w tym publikacje takie jak Modern, zwraca uwagę na rewolucję automatyzacji zachodzącą w magazynach i centrach dystrybucyjnych. Obiekty, które tradycyjnie opierały się na ludziach i wózkach podnośnikowych, obejmują konwencjonalną automatyzację, taką jak przenośniki, automatycznie kierowane pojazdy, systemy wahadłowe i technologie automatycznego przechwytywania danych, a także elastyczną automatyzację i nowe technologie, takie jak autonomiczne roboty mobilne (AMR), roboty do kompletacji elementów, autonomiczne wózki widłowe oraz technologie rzeczywistości rozszerzonej (AR) i rzeczywistości wirtualnej (VR).
To była ekscytująca jazda. Ale możesz wybaczyć producentom zbiorowe ziewanie: w końcu automatyzują oni od dziesięcioleci, w tym zautomatyzowane magazynowanie, roboty i pojazdy autonomiczne. Ciągłe doskonalenie i transformacja — koncepcja dekonstrukcji, a następnie przeprojektowania procesów w celu wyeliminowania czasu, kroków i pracy bez wartości dodanej — to standardowa procedura operacyjna dla producentów takich jak Guardian Industries.
„Transformacja jest częścią naszej kultury”, mówi Peter Westrick, kierownik ds. transformacji produkcji w zakładzie Guardian Industries o powierzchni 121 920 metrów kwadratowych w Evansville w stanie Indiana. Zawsze szukamy sposobów na utrzymanie lub zwiększenie przepustowości dzięki automatyzacji, aby poprawić wkład, jaki poszczególne osoby wnoszą do tworzonej przez nas wartości”.
Podczas gdy projekty transformacyjne są w toku i obejmują wiele procesów, ostatnim projektem było wdrożenie autonomicznych, mobilnych holowników wykorzystujących nawigację wizyjną lub kamerową (Seegrid) do przenoszenia materiałów z obszaru magazynowego w zakładzie do komórek produkcyjnych, a następnie puste pojemniki lub gotowe produkty z powrotem do magazynu. Pojazdy przyniosły szereg kluczowych korzyści, zauważa Arvind Ajayakumar, inżynier strumienia wartości, który również pracował nad projektem.
- Bezpieczeństwo: automatyczne holowniki eliminują zmienność operatora; za każdym razem wykonują te same zakręty w ten sam sposób i zawsze jeżdżą z bezpieczną prędkością.
- Skalowalność: Automatyzacja umożliwia Guardian Industries zwiększenie działalności bez takiego samego procentowego wzrostu nakładu pracy. To ważne na napiętym rynku pracy.
- Powtarzalność i przewidywalność: Automatyzacja umożliwia przewidywalne i spójne dostarczanie do gniazd produkcyjnych, dzięki czemu nigdy nie brakuje im części, ponieważ operator holownika nie dostarczył materiału na czas.
Tworzy możliwości ulepszania pracowników: Trudna do zmierzenia, ale ważna dla kultury Guardian Industries, jest możliwość ulepszania pracowników, którzy byli zaangażowani w procesy ręczne, takie jak obsługa holownika. „Kiedy automatyzujemy, stwarzamy jednostkom możliwość podniesienia poziomu lub ulepszenia swoich umiejętności w organizacji” — mówi Westrick. „Dzisiaj przenoszą produkt. Jutro mogą podejmować decyzje dotyczące sposobu działania robotów w naszym zakładzie”.
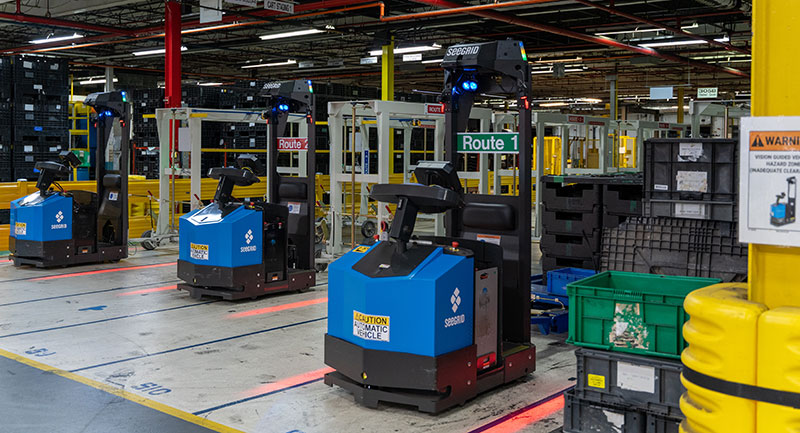
AMR stoją tutaj w kolejce, czekając na ładunek na przydzieloną im trasę
Guardian Industries, globalna firma z siedzibą w Auburn Hills w stanie Michigan, prowadzi zakłady w Ameryce Północnej i Południowej, Europie, Afryce, na Bliskim Wschodzie iw Azji. Firmy Guardian zatrudniają 14 000 osób i produkują wysokiej jakości szkło; wyroby ze szkła powlekanego i prefabrykowanego do zastosowań ze szkła architektonicznego, mieszkalnego, wewnętrznego, transportowego i technicznego; oraz wysokiej jakości chromowane i malowane elementy z tworzyw sztucznych dla przemysłu samochodowego i ciężarówek.
Fabryka w Evansville dostarcza samochodowe elementy wykończenia ze specjalnymi wykończeniami, takimi jak lakierowanie i chromowanie.
Projekt dla sukcesu automatyzacji
Podczas gdy niektórzy dostawcy motoryzacyjni działają na zasadzie just-in-time, just-in-sequence, wysyłając określone ilości zamówienia co 90 minut i w kolejności wymaganej na linii montażowej, Guardian Industries jest zobowiązana do wysyłania zamówień codziennie od prognozy swoich klientów oraz utrzymanie uzgodnionych terminów realizacji i ilości zapasów w każdej odpowiedniej lokalizacji.
Mapowanie strumienia wartości i ciągłe doskonalenie są stałym elementem branży motoryzacyjnej, która nieustannie dąży do usprawnienia procesów, zmniejszenia robocizny, wyeliminowania odpadów do kontroli i obniżenia kosztów. „Przyglądamy się wszystkim strumieniom na poziomie makro w organizacji, aby usprawnić nasze procesy i opracować skalowalne systemy, abyśmy mogli rozwijać naszą działalność bez takiego samego wzrostu nakładu pracy” — mówi Westrick.
Automatyzacja procesów ręcznych tam, gdzie to możliwe, jest częścią mapowania strumienia wartości, ale wymaga innego działania firmy Guardian Industries. Roboty, takie jak na przykład autonomiczne, mobilne holowniki, są spójne i niezawodne, ale wymagają również spójnego i przewidywalnego środowiska operacyjnego.
„W przeszłości, jeśli komórka potrzebowała materiałów i operatorów, można było po prostu wezwać kierowcę wózka widłowego i za kilka minut ładunek byłby tam”, zauważa Ajayakumar. „Teraz musimy inaczej myśleć o tym, jak planujemy dzień po dniu, i myśleć o celu”.
Westrick dodaje: „Zmusza nas to do spojrzenia na obiekt z lotu ptaka i zadawania pytań: W jaki sposób możemy dostosować układ w celu uzyskania wyższego wskaźnika sukcesu przy użyciu automatyzacji?” Na przykład przeprojektowanie układu i lokalizacji gniazd produkcyjnych może skrócić czas podróży, co nie tylko przyspiesza dostawę do gniazd produkcyjnych, ale może również zmniejszyć liczbę pojazdów wymaganych do nadążania za tempem produkcji i przepustowością.
Podczas gdy Covid zaostrzył wyzwania operacyjne w zakładzie, zwiększając możliwości automatyzacji, praca była problemem już przed pandemią. „Nasz wskaźnik rotacji jest prawdopodobnie nieco wyższy w przypadku obsługi materiałów niż w przypadku bezpośredniej siły roboczej na linii”, mówi Westrick. „Ale zaczęliśmy przyglądać się tym projektom automatyzacji przed Covid”.
Od widelców po holowniki
Według Ajayakumara projekt był już w toku, kiedy dołączył do firmy przed Westrickiem w 2019 roku. Decyzja o automatyzacji została już podjęta, a cele ustalone. Firma Guardian Industries chciała stworzyć szczuplejszy, bezpieczniejszy, bardziej wydajny i skalowalny system.
Praca była również kluczową siłą napędową w Evansville, gdzie znajduje się wiele producentów i centrów dystrybucji, z których wszyscy konkurują o tę samą ograniczoną pulę talentów.
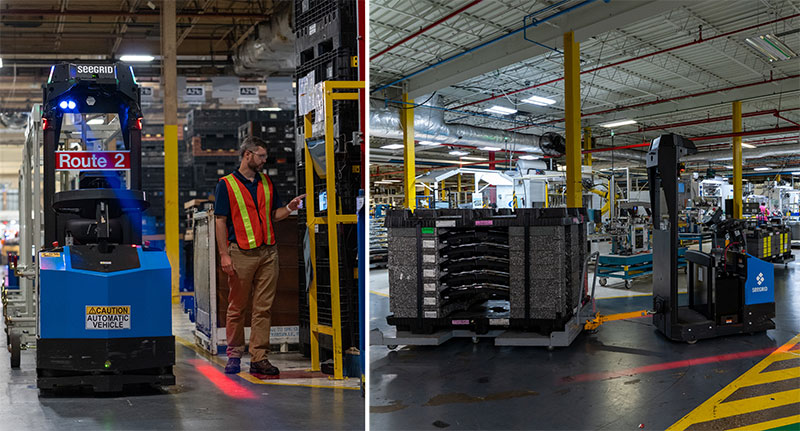
Operator przypisuje miejsce zwrotu w zrobotyzowanym systemie operacyjnym (po lewej). AMR z ładunkiem na wózku automatycznie jedzie do miejsca nadania (po prawej).
„Po pierwsze zmagaliśmy się z ograniczeniem siły roboczej” — mówi Ajayakumar. „Nasze ręczne procesy nie były powtarzalne, co prowadziło do przestojów na linii, jeśli dostawy materiałów nie były spójne lub terminowe. Istniała też zmienność w sposobie, w jaki ręczni kierowcy obsługiwali ciężarówki, zwłaszcza gdy odbywały się na zmianę. Nie było tak bezpiecznie, jak chcieliśmy.
Chociaż podjęto decyzję o automatyzacji, przejście z wózków widłowych na zautomatyzowane ciągniki odbywało się etapami. Dostawy były początkowo realizowane za pomocą wózków widłowych. W drugiej fazie firma Guardian Industries wprowadziła ręczne holowniki i wózki. Pomysł polegał na użyciu ręcznych holowników przez okres pięciu lat, aby zrozumieć układ i zmiany behawioralne, które byłyby wymagane do przejścia na automatyzację.
Do tego czasu wybrano również dostawcę rozwiązania. Jednym z najważniejszych czynników decydujących był system nawigacji oparty na kamerach, łatwość planowania tras i elastyczność. „W porównaniu z innymi rozwiązaniami AMR, używane przez nas holowniki mogą w razie potrzeby obsługiwać wiele wózków i większą ładowność”, mówi Ajayakumar.
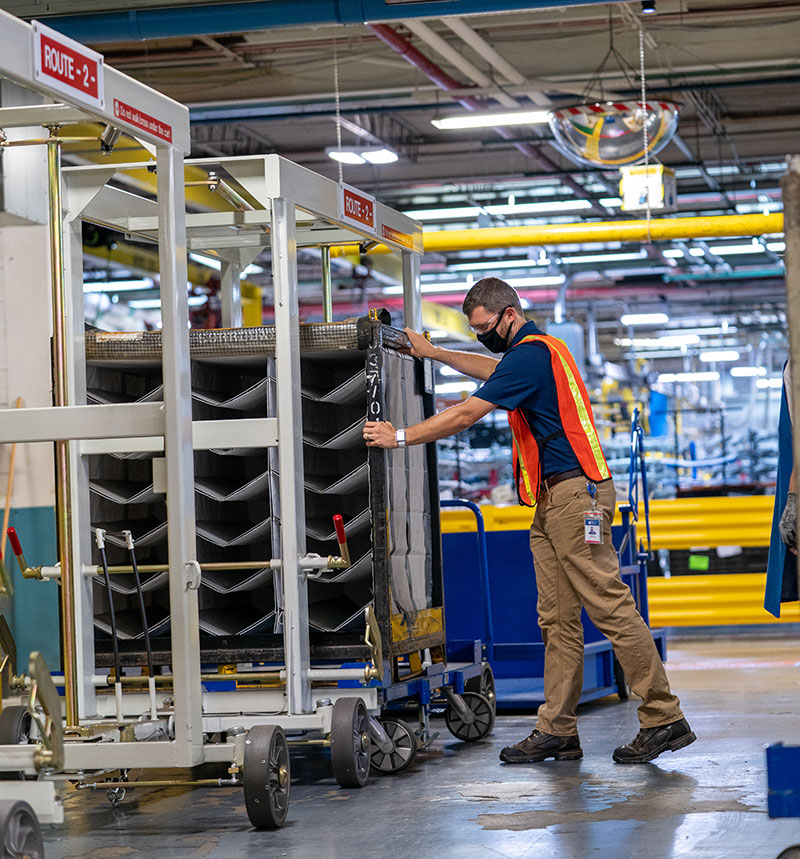
Tutaj operator przygotowuje kolejny wózek do dostarczenia do miejsca nadania na linii produkcyjnej.
Innym kryterium była możliwość integracji z systemem zarządzania produkcją (MES) Guardian Industries. Nie zostało to jeszcze osiągnięte, ale według Westricka jest to na mapie drogowej na przyszłość.
Wiosną 2019 roku Guardian Industries był gotowy do wprowadzenia autonomicznego holownika dla pilota.
Od pilota do wdrożenia
Pierwszy pojazd pilotażowy został odebrany w marcu 2019 roku. Plan zakładał wykorzystanie pojazdu do obsługi jednej trasy przez około trzy miesiące, a następnie, zakładając, że pilot się powiódł, wykorzystać wnioski pilota do dalszego wdrażania.
Przed sprowadzeniem pojazdu do zakładu firma Guardian Industries współpracowała z firmą Seegrid w celu oceny materiału na trasie. Na miejscu zaprogramowanie trasy zajęło około trzech dni, a kolejny tydzień na przeszkolenie pojazdu na trasie. Następnie odbyła się sesja szkoleniowa dla pracowników, od hali produkcyjnej po kierownictwo, na które pojazdy miałyby wpływ.
„Mieliśmy dedykowane sesje szkoleniowe na temat obsługi pojazdów i ich funkcji bezpieczeństwa”, mówi Ajayakumar. „Współpracowaliśmy z operatorami, aby zaprojektować trasy, liczbę części w każdej komórce i zaplanować harmonogram, aby uwzględnić wolniejszą prędkość pojazdów autonomicznych”.
Ajayakumar dodaje, że niektórzy członkowie zespołu obawiali się, że automatyzacja zastąpi ich pracę, „ale było to zapośredniczone zaangażowaniem na sali”. Członkowie zespołu mogli zobaczyć, że pojazdy otworzyły pracownikom ds. zarządzania materiałami możliwości przeniesienia się do obszarów o wartości dodanej w zakładzie, a po drugie dostrzegli możliwość doskonalenia swoich umiejętności, ponieważ zdobywali doświadczenie w obsłudze bardziej zaawansowanych technologii robotycznych.
Niektóre ograniczenia fizyczne i technologiczne ograniczały liczbę wózków, które mogły być obsługiwane przez autonomiczne holowniki, zwłaszcza jeśli chodzi o skręcanie. Jednym z nich były stosunkowo wąskie szerokości korytarzy, a drugim wykorzystywana wówczas technologia wózków.
„Na początku mogliśmy holować tylko dwa do trzech wózków na raz” — mówi Ajayakumar. „Dzięki ulepszonej technologii wózków i pracy z systemem możemy teraz holować od pięciu do sześciu wózków, a w niektórych przypadkach nawet do siedmiu lub ośmiu”.
Pilot leciał szybciej niż przewidywano. W ciągu trzech tygodni działalności Guardian Industries zaczął dyskutować, jak wykorzystać dodatkowe trasy obsługiwane przez ręczne holowniki. Sprowadzono personel operacyjny z innych fabryk, aby zobaczyć, jak przebiega projekt, ponieważ ostatecznym celem było rozszerzenie zastosowania autonomicznych holowników na lokalizacje w Kentucky i Missouri.
Praca z automatyzacją
Guardian Industries pracuje z autonomicznymi holownikami od nieco ponad dwóch lat. Proces rozpoczyna się, gdy operator w komórce produkcyjnej przesyła zamówienie na części do systemu MES.
Ponieważ MES i system zarządzania flotą nie są jeszcze zintegrowane, zamówienie jest wysyłane na tablety używane przez współpracowników w magazynie. Każda część składowana w magazynie jest powiązana z konkretną lokalizacją w obszarze produkcyjnym, a co za tym idzie unikalną trasą.
Po załadowaniu wszystkich pojemników z dostawą na trasę na wózki, pracownicy uzyskują dostęp do systemu nawigacji floty na swoich tabletach, gdzie znajduje się szereg przycisków. Każdy przycisk jest specyficzny dla części i trasy. Współpracownicy następnie wybierają przycisk, który jest odpowiedni dla tej dostawy, a pojazd rozpoczyna trasę. Po dotarciu na miejsce operatorzy w komórce produkcyjnej rozładowują części, a następnie ładują puste pojemniki lub gotowe części na wózek w celu powrotu do magazynu.
Guardian Industries kontynuuje naukę — jest to część jej inicjatyw ciągłego doskonalenia i mapowania strumienia wartości. Po pierwsze, zespół kontynuuje współpracę z Seegrid nad integracją systemów, tak aby zamówienia trafiały bezpośrednio z MES do systemu nawigacyjnego. Obecnie planowany jest na I kwartał 2022 roku.
Firma wykorzystuje również system symulacji planowania tras do projektowania tras, które mogą pomieścić większą liczbę pojazdów eksploatowanych w zakładzie. „Kiedy skalowaliśmy system, stwierdziliśmy, że planowanie tras było bardziej skomplikowane, ponieważ istniały teraz interakcje między pojazdami autonomicznymi a innymi pojazdami w zakładzie”, mówi Ajayakumar. „To nie zostało uchwycone w pilocie”.
Oprogramowanie umożliwia firmie Guardian Industries symulowanie tras na większą skalę i identyfikowanie potencjalnych wąskich gardeł dla pojazdów, oszacowanie liczby wózków potrzebnych na każdą trasę oraz dokładniejsze określenie poziomu pracy ręcznej wymaganej do wymiany materiałów między pojazdami.
Po drugie, automatyzacja ujawniła możliwości usprawnienia procesów, które zostały pominięte, gdy procesy były wykonywane ręcznie. „W przeszłości, jeśli popełniliśmy błąd lub nie zaplanowaliśmy dobrze produkcji, kierowca wózka widłowego mógł znaleźć brakujące komponenty i dostarczyć je na linię produkcyjną”, mówi Westrick. „Mieliśmy opatrunek, który pozwolił nam zrekompensować problemy. Teraz koncentrujemy się na byciu proaktywnym, a nie reaktywnym, rozwiązując podstawowe problemy, a nie je obchodząc. Koncentrujemy się na wyższym celu"
„W dłuższej perspektywie" – dodaje – „zmniejszymy zmienność naszych operacji i będziemy mieć mniej uszkodzeń naszego produktu."
Przeprojektowanie pod kątem wydajności
Autonomiczne holowniki automatyzują dostarczanie części na linię.
- Rozpoczęcie procesu W gniazdach produkcyjnych znajdują się dwa pojemniki na wyroby gotowe. Jeden to aktywny pojemnik, a drugi to pojemnik na bufor. Gdy tylko aktywny pojemnik jest pusty, operator wysyła sygnał do magazynu materiałów, że potrzebne są części.
- Przygotowanie koszyka W międzyczasie zaprogramowane trasy zostały zmapowane i wprowadzone do systemu nawigacji robota, a wózki są ustawiane na parkingu. Pracownicy magazynu otrzymują instrukcje na swoich tabletach i zaczynają pobierać wymagane numery części z magazynu i ustawiać pojemniki na wózkach. Gdy wszystkie pojemniki na trasę są gotowe i załadowane na wózek, operator wybiera numer trasy w systemie zarządzania, a pojazd jest gotowy do podróży do miejsca dostawy.
- Dostawa Pojazd zatrzymuje się w wyznaczonej komórce produkcyjnej. Tam operator rozładowuje materiały, a następnie ładuje puste pojemniki lub gotowe produkty na wózek. Następnie pojazd wraca do magazynu.
Źródło mmh - Bob Trebilcock